- 04 mei 2023
- Door Harm Ikink
NAAR CIRCULARITEIT IN PE EN PP VERPAKKINGSPLASTIC
SLUITEN VAN KRINGLOOP ‘PMD POLYOLEFINES’ IS NOG MOEILIJK
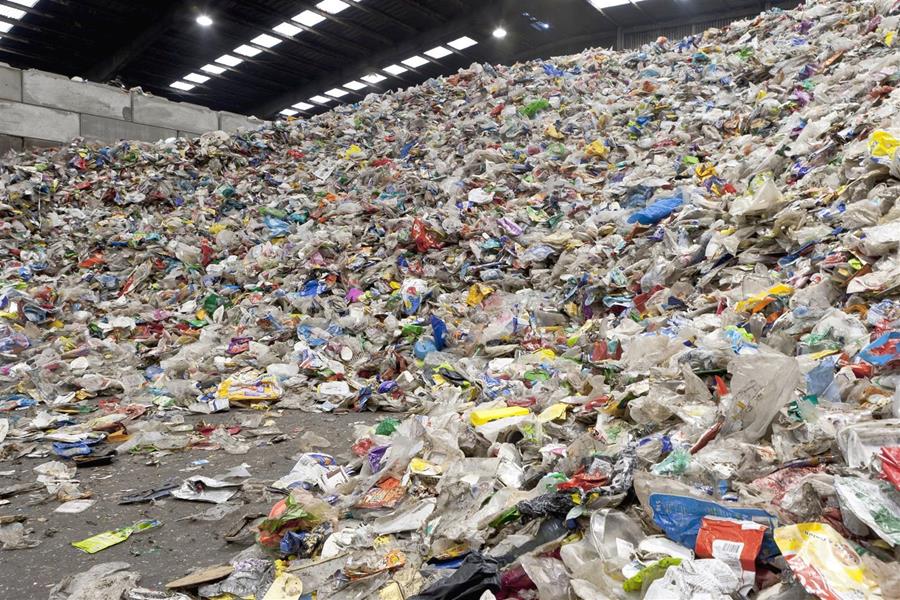
Het recyclen van de pmd-afvalstroom is een enorme uitdaging. Na sortering krijg je een mixed plastics stroom (DKR350) waarvoor pyrolyse een geschikte verwerkingstechnologie lijkt. Maar uit recent afgerond onderzoek binnen het Circular Plastics Initiative (CPI) van ISPT en DPI blijkt dat geen haalbare kaart. Het pyrolyseproduct bevat te veel halogenen en zuurstof om als feedstock voor nieuwe plastics te dienen. De oplossing ligt in betere plastic scheiding vooraf, nabehandeling van de pyrolyseolie, of alternatieve verwerking via vergassing. Of liever nog, in design for recycling.
Een aantal plants is al operationeel op kleine industriële schaal met een omvang van enkele tientallen kiloton
nieuwe kansen
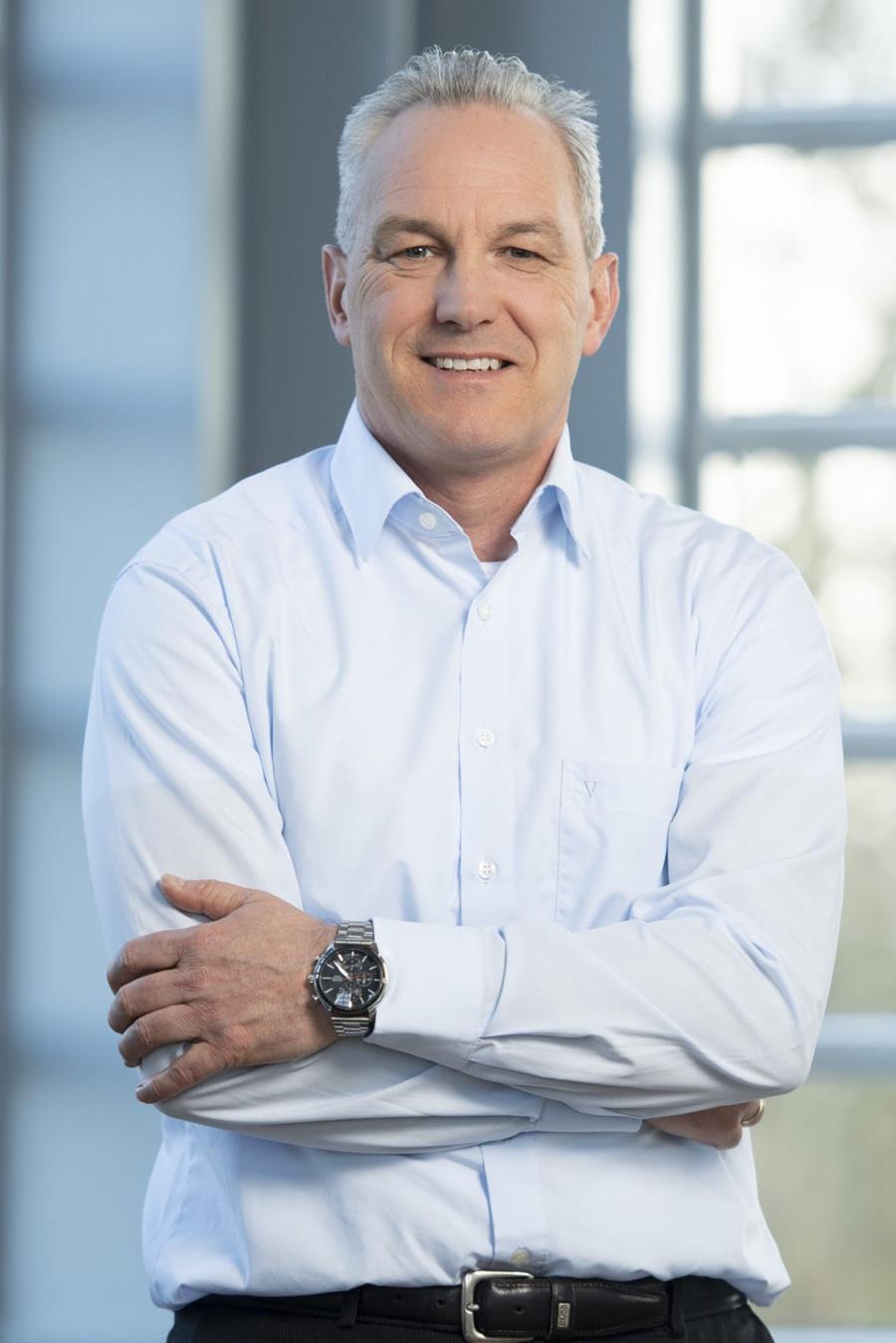
Tweeëneenhalf jaar hard werken. Samen met plastic producenten, product designers, plasticverwerkers, afvalinzamelaars, afvalscheiders, procestechnologen en polymeerexperts. En dan concluderen dat het niet lukt. Dat was zeker wel even slikken voor projectleider Ronald Korstanje, programmadirecteur CPI? “Dat valt wel mee”, luidt het opgewekte antwoord. “Als je uitgaat van de pmd-stroom uit huishoudelijk afval, dan weet je dat het lastig gaat worden. Maar die uitdaging zijn we aangegaan. We hebben alle stappen in de keten met elkaar in verbinding gebracht en we hebben enorm veel geleerd. We weten nu beter waar nog aan gewerkt moet worden om de kringloop te kunnen sluiten.”
Korstanje zegt dat bij de start van het project, in mei 2020, plastic recycling nog in de kinderschoenen stond. “Er was eigenlijk geen gezamenlijkheid, iedereen had zijn eigen benadering, men kende elkaars technologie niet en men sprak niet dezelfde taal.” Dat is echt helemaal veranderd: “Er is nu samenwerking tussen verschillende partijen, er is wederzijds inzicht. Daardoor ziet men mogelijkheden de eigen prestatie te verbeteren en ontstaan er nieuwe kansen.”
plastic fracties
Polyolefines, met name polyetheen (PE) en polypropeen (PP), zijn veruit de meest gebruikte verpakkingsplastics voor allerlei uiteenlopende producten. Van de folie om de komkommer tot de bakjes van de champignons, en van de trays voor viooltjes bij het tuincentrum tot de zakjes met spijkers van de bouwmarkt. Dat komt allemaal in de containers voor plastic, metaal en drankpakken, kortweg pmd. Afvalinzamelaars halen die leeg, en na een eerste scheiding levert dat afzonderlijke afvalstromen met drinkpakken, metalen, en dus ook plastics. De sorteerinstallaties scheiden verschillende plastic fracties die worden aangeduid als DKR310 (folies) en DKR350 (gemengde kunststoffen). Die laatste is een hele lastige fractie want behalve PE en PP is daarin ook pet, en soms zelfs pvc te vinden.
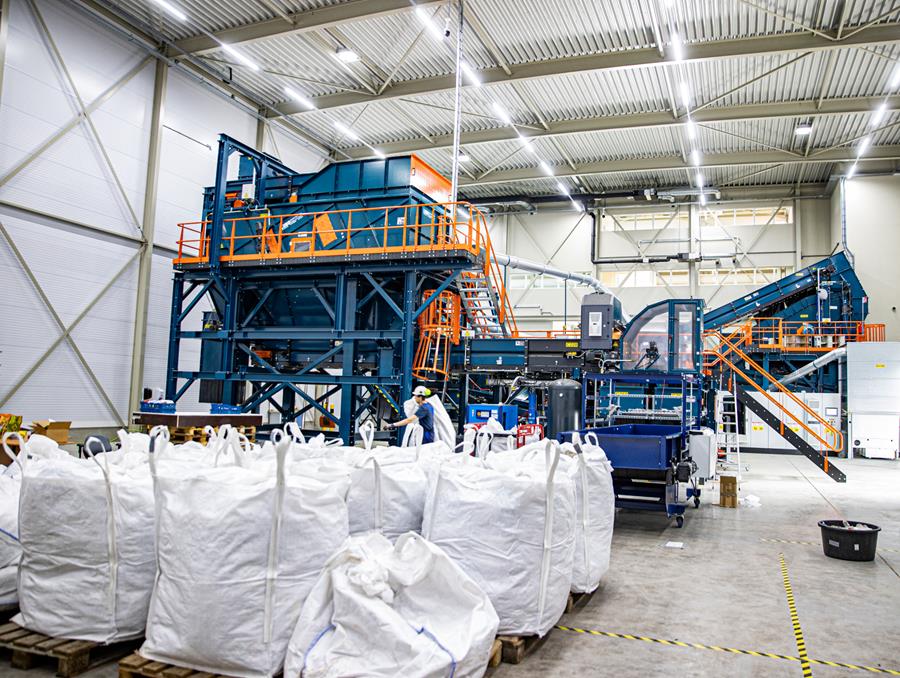
Pyrolyse
Het CPI-onderzoek richtte zich op de verwerking van deze DKR350-stroom via thermochemische recycling (zie kader) en dan met name pyrolyse. Daarbij wordt het plastic kort en snel verhit tot 400-550 graden in de afwezigheid van zuurstof, waarbij de polymeerketens vrij willekeurig worden opgebroken. Het resultaat is een olie (soms een wax) die bestaat uit een mengsel van korte ketens. Het is een bekende, industrieel beschikbare technologie en er zijn inmiddels meerdere technologie-aanbieders. Een aantal plants is al operationeel op kleine industriële schaal en er is een veelvoud aangekondigd. De typische omvang van deze plants is enkele tientallen kiloton. Naar verwachting zullen volledig commerciële plants een omvang hebben van 50-200 kiloton.
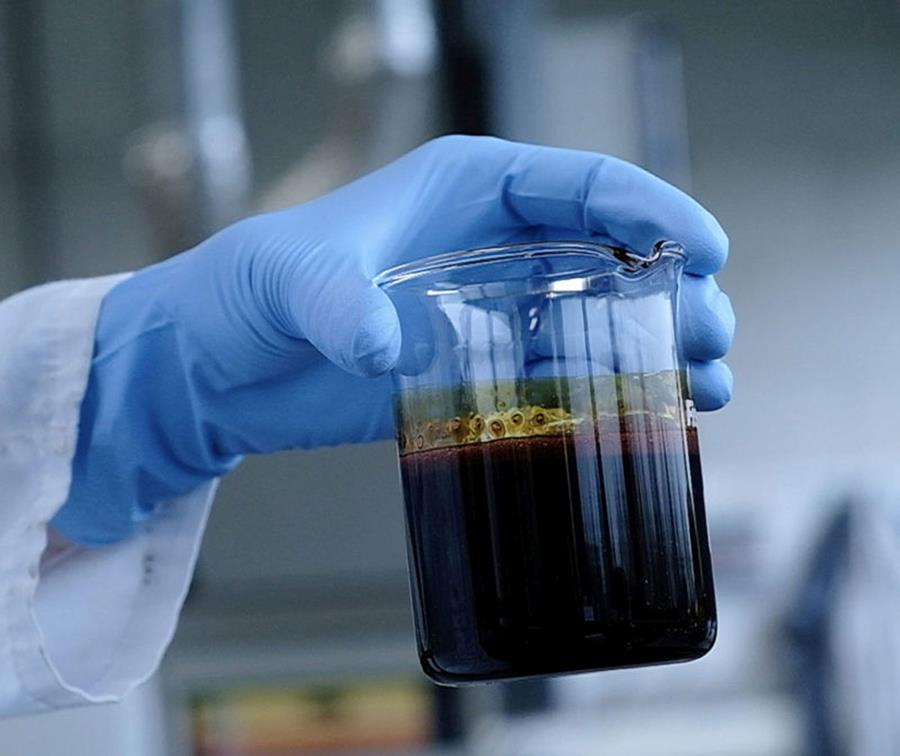
De verwachting is dat de DKR310-foliestroom zich goed laat pyrolyseren, omdat het een redelijk goed gedefinieerde stroom is. Korstanje: "Er waren claims dat DKR350 ook te verwerken zou zijn, maar het ontbrak aan duidelijke wetenschappelijke resultaten. We hebben nu voor het eerst duidelijk vastgesteld dat de DKR350 gesorteerde stroom zoals deze nu beschikbaar is niet geschikt kan zijn voor pyrolyse."
CHEMISCH RECYCLEN
Het idee van chemisch recyclen is dat je het polymeer afbreekt tot moleculaire bouwstenen voor nieuwe plastics. Dat kan op verschillende manieren. pet-plastic is bijvoorbeeld een polycondensaat dat relatief gemakkelijk chemisch is af te breken, via hydrolyse (afbreken onder invloed van water), of met enzymen. Het lastige van polyolefinen is dat ze geen ‘aangrijpingspunten’ in de polymeerketen hebben om zulke depolymerisatie mogelijk te maken. Die moet je thermisch kraken, ook wel thermochemisch recyclen genoemd. Pyrolyse is daarvoor een geschikte technologie. Het levert een product dat nafta uit aardolie kan vervangen. Een naftakraker maakt er dan etheen en propeen van, daar kun je weer nieuwe polymeren van maken, waar vervolgens weer plastics van gemaakt worden. Deze benadering lost ook het probleem op dat het bij PE en PP in feite uit honderden zo niet duizenden verschillende plastics gaat. Voor elke gewenste eigenschap (transparantie, kleur, stevigheid, gasdichtheid, etc.) worden allerlei stoffen aan het polymeer toegevoegd. Die maken het zo goed als onmogelijk om deze plastics mechanisch te recyclen (ingezamelde producten vermalen, regranuleren en tot nieuwe producten verwerken).
Lees ook: Pyrolyse-olie als alternatief voor aardolie en -gas
Te veel chloor en zuurstof
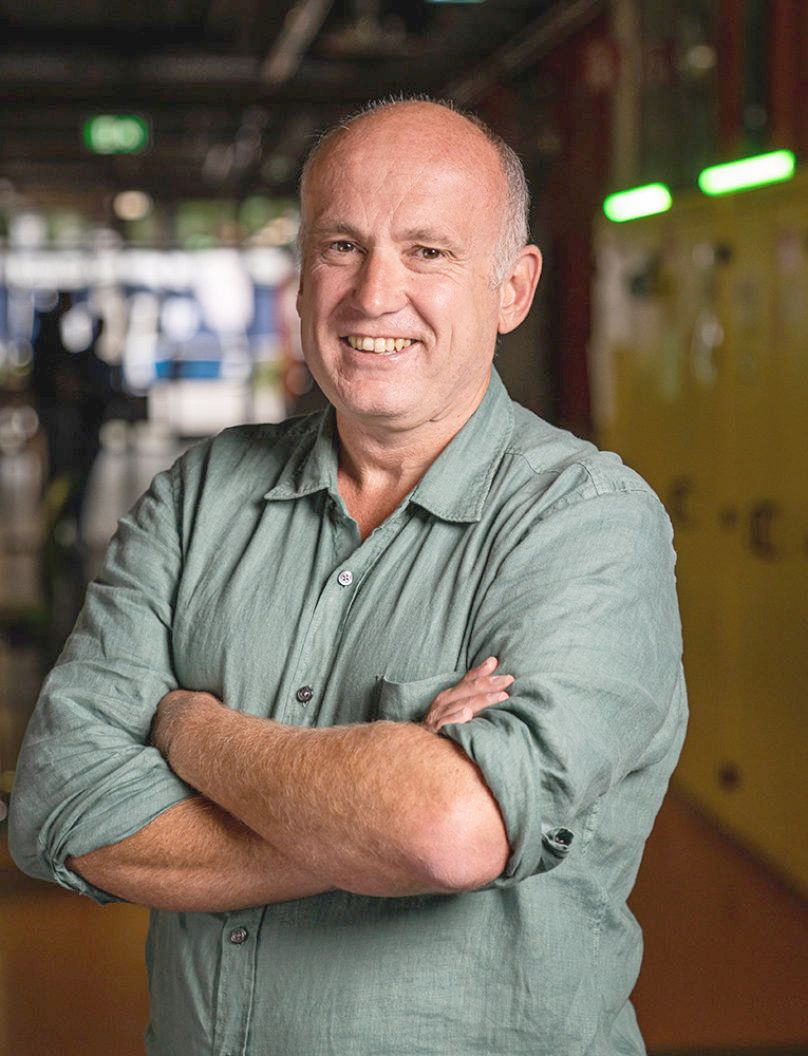
Sascha Kersten, hoogleraar Duurzame Procestechnologie aan de Universiteit Twente en leider van deze deelstudie legt uit: "De atoombalans speelt ons parten: wat er aan atomen van een bepaalde soort de installatie ingaat, komt er altijd ook weer uit. We hebben veel metingen gedaan en analyses uitgevoerd om vast te stellen wat erin zit en wat daarmee gebeurt. Vind je verontreinigingen terug in de pyrolyse-olie, het gas, het vaste residu? Helaas hebben we moeten vaststellen dat je vooral te veel chloor en zuurstof in de pyrolyseolie tegenkomt. We hebben geen manier kunnen vinden om de DKR350-afvalstroom in één keer om te zetten naar een product dat kan worden bijgemengd in naftakrakers. Er is nog een hydrogenatie en purificatiestap nodig, dus daar kijken we nu naar in vervolgstudies.”
Het is natuurlijk ook een oplossing om ervoor te zorgen dat er aan de voorkant geen chloor en zuurstof in gaat. Zuurstof is vooral afkomstig uit pet en papierresten die nog in de DKR350-stroom zitten. Kersten: "Het heeft zeker zin DKR350 een stap verder uit te sorteren. Dan is het aan te raden om de olefinerijke stroom te pyrolyseren en de residustroom te vergassen. Bij vergassing krijg je de zuurstof er eigenlijk vanzelf uit, als water, CO en CO2. Daar is ‘t als het ware ingebakken in de procesvoering."
De bottom line is dat het veel inspanning en energie zal kosten om de huidige DKR350-olefinen succesvol te kunnen pyrolyseren
RECYCLINGRENDEMENT
Voor polyolefinen zal het lastig zijn om hoge recyclingrendementen te behalen, zegt hoogleraar Kersten. Als het binnen de polyolefineketen moet blijven, dan ligt het rond de 50%. De pyrolyse heeft een rendement van ongeveer 70%, de rest van de koolstof gaat verloren in de gassen en het vaste residu. Vervolgens heeft ook een naftakraker een koolstofrendement van 70% - de rest zit in de CO2 die ontstaat bij de verbranding van de kraakgassen (met name methaan) voor de energievoorziening. Het totaalrendement is dan 70% van 70% en dat is dus net iets minder dan 50%. Kersten pleit daarom voor een ruimere blik op recyclingrendementen. “Focus op het goed hergebruik van koolstof, in plaats van op een hoog recyclingrendement binnen een specifieke productketen. Uiteindelijk gaat het niet om circulariteit voor een specifieke plasticsoort; we willen dat alle koolstof uit afvalplastics weer zinvol wordt benut.”
Design for recycling
Korstanje vertelt dat in het project ook is gekeken naar betere scheidingstechnieken. Zo is deepUV ramanspectroscopie bestudeerd, waarbij zeer kortgolvige uv-straling wordt gebruikt zoals ASML gebruikt in hun chipmachines. "We hebben vastgesteld dat je daarmee bijvoorbeeld zwart plastic kunt karakteriseren en sorteren, wat tot nu toe vaak een heikel punt is."
Daarnaast is gewerkt met een nieuw algoritme dat werd ontwikkeld bij de chemometriegroep van de Radboud Universiteit. "Dat maakt het mogelijk om sneller en accurater plasticsoorten te kunnen herkennen en sorteren." In dit deel van het project is nauw samengewerkt met het Nationaal Testcentrum Circulaire Plastics (NTCP) in Heerenveen, dat net was opgeleverd toen het project begon. Ook producenten van sorteermachines waren bij het onderzoek betrokken.
De bottom line is echter dat het veel inspanning en energie zal kosten om de huidige DKR350-olefinen succesvol te kunnen pyrolyseren. Volgens Korstanje is het zonneklaar dat het design van PE- en PP-verpakkingen cruciaal is. “Uiteindelijk zal je helemaal op recycling moeten ontwerpen. Tot het zover is, zal het heel moeizaam gaan om goed gedefinieerde stromen beschikbaar te krijgen voor succesvolle thermochemische recycling.”
Kersten: "Het plastic zoals we dat nu gebruiken, is geoptimaliseerd voor een bepaald gebruiksfunctie, tegen de laagst mogelijke kosten. Daarbij is nooit nagedacht over recyclen. Want als je broomhoudende vlamvertragers gebruikt, dan krijg je een broomfractie in je pyrolyse-olie. Zo zitten we ook met de chloorfractie die afkomstig is uit pigmenten. Vooral groene pigmenten kunnen wel tot vijftig massaprocent chloor bevatten. En zelfs de meest simpele verpakkingen bevatten meerdere plastics, zodat je eigenlijk nooit een monostroom hebt. We moeten echt gaan nadenken wat er moet veranderen om ervoor te zorgen dat je de cirkel echt kunt sluiten, dat je materialen kunt terugvoeren naar het begin van de keten. Want je kunt wel concluderen dat ons huidige plastic daar nu niet geschikt voor is.”
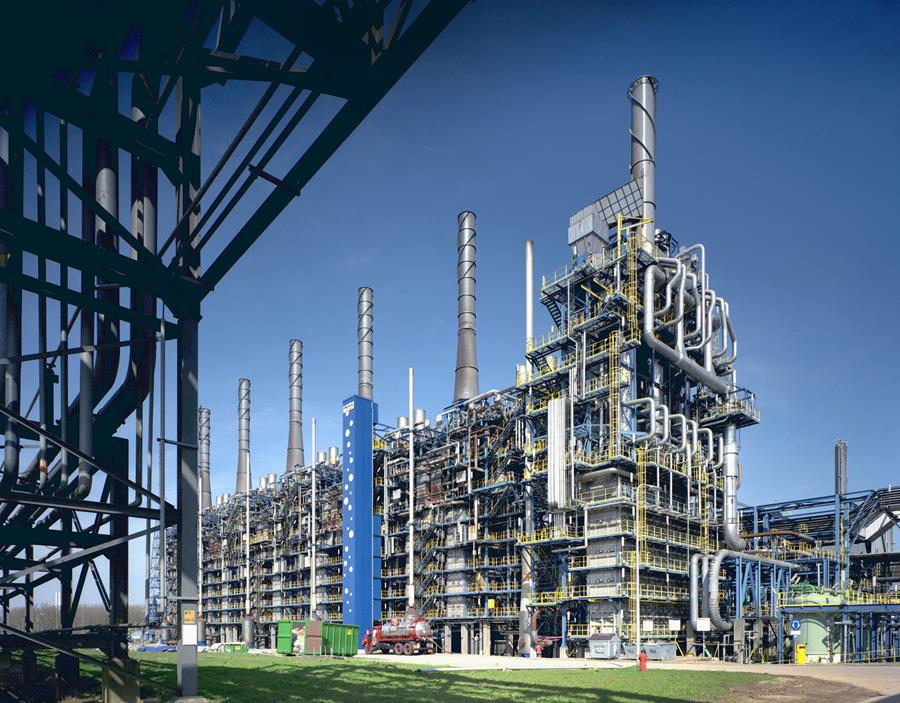
Plastic is geen aardolie
Korstanje heeft goede hoop dat er verbetering gaat komen: alle deelnemers in het project zien de urgentie en ze werken bijna allemaal mee aan vervolgprojecten. Kersten ziet zelfs een verandering bij de plasticproducenten, die eigenlijk het liefst met feedstock werken van dezelfde specificaties als aardolie - een fantastische grondstof met prima specificaties en constante kwaliteit.
Kersten: “Als je één keer gaat kijken hoe het pmd bij de inzamelaar binnenkomt en wat voor een rommel pmd-plastic eigenlijk is, dan ga je beseffen hoe lastig dat is.” Hij hoopt en verwacht dat de grote plasticproducenten bereidwilliger worden. “Natuurlijk zullen ze zolang mogelijk aan de van aardolie afgeleide specs vast willen houden. Maar we zien dat ze gaan beseffen dat ze dingen anders aan moeten pakken om succesvol deze recyclingketen voor elkaar te krijgen.”
Lees meer over het Circular Plastics Initiative
Lees meer over het onderzoek naar circulariteit in polyolefines
CIRCULAR PLASTICS CONFERENCE 2023
Op 14 juni 2023 is er de Circular Plastics Conference (CPC). Dit is hét jaarlijkse evenement rond circulariteit in plastic: van afval tot waardevolle grondstof in een circulaire economie. Met keynotes, parallelsessies en vooral veel gesprekken tussen deelnemende partijen stimuleert de conferentie de realisatie van circulariteit in kunststoffen op industriële schaal. De hele waardeketen komt aan bod, vanuit een internationaal perspectief en met het vizier op de technologische, logistieke en maatschappelijke uitdagingen. Plaats van handeling is de Jaarbeurs Meetup in Utrecht. Aanmelding via https://ispt.eu/cpc
Installaties voor pyrolyse van afvalplastics in Nederland:
• SABIC & Plastic Energy (Chemelot): 20 kton pyrolyseolie per jaar
• Pryme (Rotterdam): 30 kton pyrolyseolie per jaar
• Blue Cycle (Heerenveen): 16,5 miljoen liter pyrolyseolie per jaar
• BlueAlp & Shell (Moerdijk): 30 kton pyrolyseolie per jaar, opstart verwacht begin 2024
• Xycle (joint venture NoWit, Patpert Teknow Systems en Vopak) (Europoort): 20 kton pyrolyseolie per jaar, start bouw verwacht in 2022, opstart in 2023
• Itero (Chemelot): 19 kton pyrolyseolie per jaar, opstart verwacht in 2024
• Dow, Fuenix & Haldor Topsoe (Terneuzen): 10 kton pyrolyseolie per jaar, bouw aangekondigd
• Neste, Ravago & Alterra Energy (Vlissingen): ongeveer 38 kton pyrolyseolie per jaar, aangekondigd
• Teijin Aramid & Clariter (Delfzijl): omvang onbekend, aangekondigd. Specifiek voor supersterk (hoogmoleculair) PE (visnetten, touwen, luchtvaartcontainers).
(bron: Chemie Magazine, VNCI)
Lees ook: SABIC zet in op chemische recycling van kunststoffen
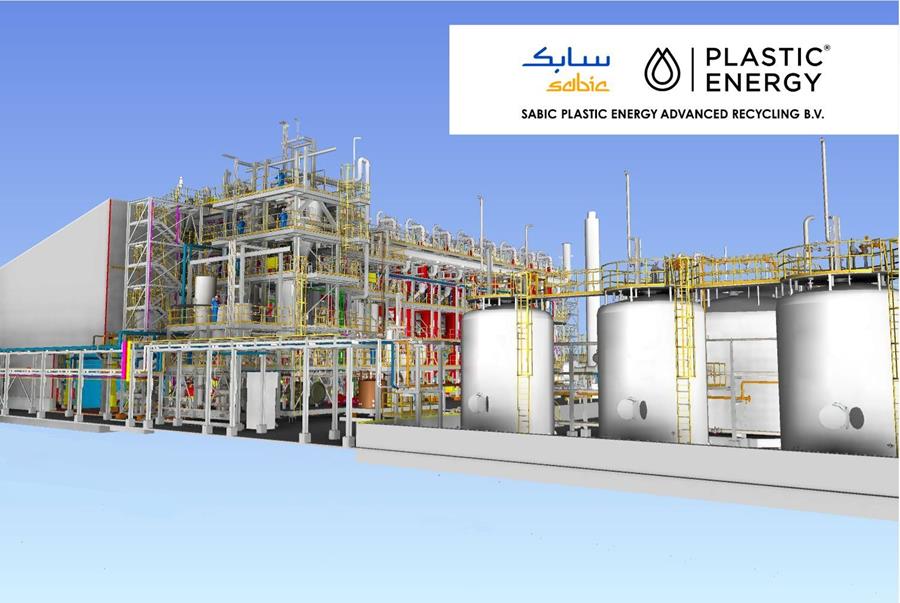